The 2024 Repair
On December 8, 2023, the Chair of the Clock Winding Committee summarized the State of the Clock to the committee in the following manner:
On December 8, 2023, the Chair of the Clock Winding Committee summarized the State of the Clock to the committee in the following manner:
"Happy Holidays! It's been a pretty non-eventful year from a clockwinding perspective, which means that it's been an excellent year for Cranbury's historic Tower Clock!
That comment would come back to haunt both the Chair and the Committee. Only a week later, on December 15, two clockwinders met in the attic of Town Hall to wind and lubricate the clock. The striking train was wound without incident, but as soon as they began winding the timekeeping train they knew something was seriously wrong. It wound smoothly, but there were no clicking sounds! The little "pawl" or "click" was not engaging the ratchet wheel. If the clockwinder took his hands off the crank or removed the crank from the arbor, the great wheel would have spun rapidly backwards and the box of gravel powering the timekeeping train would have plummeted to the attic floor.
After lowering the box of gravel onto a nearby 5-gallon bucket containing extra gravel, a quick inspection revealed the problem: the machine screw which held the click in place was very loose. How loose? The photo on the left shows the loose screw that affixes the click on the timekeeping train. The photo on the right shows the tightly fastened screw that affixes the click on the striking train.

In order to repair the problem, one of the clockwinders left and returned with a stubby, flat-head screw driver. The machine screw was tightened, the timing train was wound and everything appeared to be in fine working order. But a nagging doubt remained. The clock had been completely restored over 6 years ago and had been running without serious incident ever since. What caused this screw to come loose now? Would other screws start to come loose as well? To address those questions, the Chair posted a message on the Tower Clock forum on the NAWCC website asking for advice:
Any ideas what could have caused this particular screw to loosen? Does it indicate a systemic problem of some sort with the clock? The screw appears to work perfectly and isn't stripped. Would it be counterproductive to put a little Loctite on it?
A respected member of the forum quickly replied that a bit of Blue Loctite would probably solve the problem. The Committee considered this course of action, but decided instead to monitor the machine screw closely and see if the problem re-occurred. We didn't have long to wait. On February 1st, the screw once again became loose. Even worse, our attempt to apply a bit of Loctite on the screw threads went awry, locking the pawl in place and preventing the timing train from being wound. After completely removing and cleaning both the machine screw and the pawl, a subsequent, deeper inspection showed what appeared to be a nut between two gears of the winding mechanism (shown below):

The Committee now believed that the offending machine screw had been held tightly in place by an internal lock nut that fit somehow inside a cavity in one of the gears. We posted this new information on the Tower Clock forum and received the following confirmation from Peter Nunes, the moderator of the Forum:
"My recollection is that that the shouldered machine screw that holds the pawl in place has a nut on the inside end that acts as a lock nut. Likely that nut has fallen off, and the maintaining power wheel has moved a bit."
It was now clear that resolving this problem was outside the abilities of the Clock Winding Committee and required a tower clock professional. We notified the Township Administrator and we were advised to move forward with the repair as long as the cost was under $1,000. Anything above that would require additional approvals.
The Repair of the Clock
Our first thought was to contact Connecticut Timekeepers, the fantastic little company that restored our clock back in 2017. Sadly, that company was out of business, a victim of the COVID pandemic. Their phone was disconnected and their web presence was gone. As a last resort, we texted the owner using the number he gave us back in 2017. A day later, he responded and asked for additional information. We quickly texted it to him and, two days later, he responded saying he was no longer in the tower clock repair business and wasn't interested in the job.
Undeterred, we reached out to the few other clock repair companies in the northeast, but came away empty. One vendor responded that the repair was "outside my wheelhouse". Another vendor said he didn't possess the expertise, but had a subcontractor in New York City who could come to Cranbury, take the clock apart, bring it back to New York, fix it in his shop and reassemble it in Cranbury for a cost of $10,000. Two other vendors simply did not respond.
While all this was going on, we continued to provide Peter Nunes of the NACCW with updates. In reply to one of these updates, Peter mentioned that he owned a company called Old School Antiques in Rhode Island that repaired local tower clocks, and that he, himself, maintains an E. Howard Model 0 striking clock in his home town! Upon hearing this extremely serendipitous news, the Committee asked Peter if he would be willing to travel to Cranbury to fix our clock. At first Peter declined, saying he didn't want to waste Cranbury's money and that our problem was an easy fix. We simply had to disassemble and re-assemble half of the clock, a job that would take only "a few hours". After convincing Peter that the Committee had neither the desire nor the expertise to tinker with Cranbury's precious, historic heirloom, he agreed to take the job under the following conditions. We would have to wait a few weeks until his next trip to Pennsylvania (where he owns a second house) and we would have to pay his day rate of $800. Needless to say, we quickly agreed to his terms!
Peter arrived in Cranbury on March 25th at approximately 9:30am. Paul Mullen and Bill Kanawyer, current members of the Clock Winding Committee, were there to assist him where possible, provide light when needed, and learn as much as possible about how the clock was put together. Bill also took a bunch of photos to document the repair, which will be invaluable should this problem ever re-occur. Richard Kallan, a former member of the Committee was also on hand. Richard's expertise as an amateur machinist was put to good use when a replacement pin had to be milled slightly in order to be used during the repair. Richard had also milled a replacement nut should in the event that the original nut was not within the clock. Thankfully, his nut wouldn't be needed. Within 30 minutes of his arrival Peter had dismantled the timing train and located the missing lock nut within the cavity of the Great Wheel of the timing train.
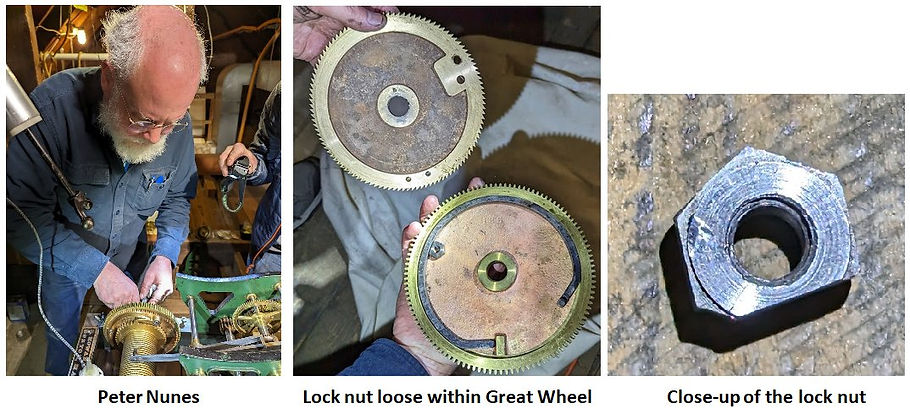
Peter them put a few drops of Loctite Blue (which he had brought with him) on the threads of the machine screw and reattached the click to the Great Wheel per the photos below. Note the orientation of the lock nut with the milled side facing the gear teeth.

Over the next two hours, Peter cleaned, reassembled, lubricated and reset the timing of our historic clock. In general, he was very impressed with its condition, but suggested we reduce our lubrication frequency from four times a year to twice a year. Other than that, the clock was in tip-top shape. We wound the timing train and, after being dormant for 51 days, the clock was ticking again!
The Bell Takes Center Stage
While Peter was in the belfry adjusting the hands of the clock, he couldn't help but notice Cranbury's equally historic 1896 McShane Foundry bell. While admiring it, he spotted a potentially disastrous condition: the bell's striking hammer was resting on the bell. Per Peter, this is something that could cause the bell to crack. As he explained, when the bell is rung, the metal vibrates. If there is an object resting on the bell, the smooth vibration pattern is disrupted, and the area around the object experiences a much higher concentration of stress. This stress can cause the bell to crack. When the hammer strikes the bell, it should immediately rebound slightly off the bell. Our hammer was not doing that because of a badly worn rubber rubber pad, as shown below.

Following Peter's advice, the Committee disabled the clock's ability to strike until a replacement pad could be found or manufactured. Bill Kanawyer, one of the Committee's original members, believed the existing rubber pad dated back to 2001 when the striking mechanism of the clock was repaired after being dormant for decades. Based on the lifespan of rubber, the existing pad was certainly not an original part from 1906 and was probably homemade. After attempting to find a replacement online, we concluded that a new pad had to be made.
First, we had to determine the type of rubber to use. It had to have the right firmness, thickness and resilience to allow the hammer to strike the bell while also causing it to recoil off the bell after the strike. After an exhaustive web search, we purchased a sheet of 3/8" 70 Shore A styrene butadiene rubber (SBR). The hardness and flexibility of this type of rubber is comparable to the sole of a shoe.
The pad is attached by two bolts to a strip of metal which function as a spring and dampens the force of the hammer's impact on the bell. To determine the exact offset and hole diameters for these bolts, clockwinder Bob Rogers removed the old pad and took a rubbing of the metal strip. As it turned out, there were two different size bolts. A nut and both washers were also missing. All of this information was turned over to Richard Kallan who then created a template which he used to produce a number of replacement pads. Richard also purchased a replacement nut and two washers, milling a section of one washer to ensure it wouldn't make contact with the shaft of the hammer during a strike.


So, how many clockwinders does it take to replace a hammer pad? The answer, apparently, is three. On the morning of April 12, 2024, Paul, Bob and Richard climbed up into the belfry and did just that. They then simulated a strike to ensure the hammer was able to effectively strike the clock and recoiled off the bell afterwards. Satisfied with the results, the ability of the clock to strike was re-enabled and, at 11:00am, the clock once again struck the hour after being silent for 69 days.
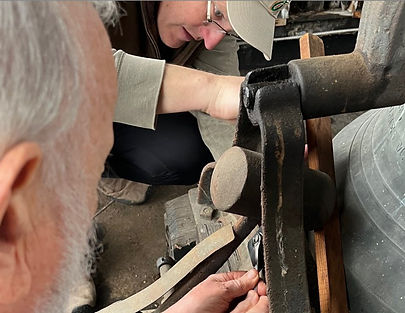
Success!

Updates to the Tower Clock Maintenance Manual
As a result of the 2024 repair, the routine maintenance procedures for the clock were updated slightly:
-
The clock will only be lubricated twice a year instead of quarterly.
-
The condition of the rubber pad in the belfry will be monitored during lubrication to ensure that the hammer is rebounding off the bell after a strike. If excessive wear is detected, the pad will be replaced immediately. The lifespan of 70 Shore A SBR is unclear, but it may be as short as 5 years.
-
The machine screw that caused the 2024 repair is the only screw in the clock with an internal lock nut. As such, this screw should be monitored regularly for any indication that it is beginning to loosen. As shown in the photo on the right, the black line drawn on the click should always be in alignment with the machine screw slot.
